CAPA Management Software
Our Corrective and Preventive Action Management Software is one of the most powerful tools available to Management to round off a systematic approach to managing their operations. The steps are logical, and they work. Most importantly, QISS-CAPA provides automation that will eliminate Waste in the process. The Waste that QISS focuses on is time. People will not waste time spent on activities that do not directly add value. They will have the time to spend on what only humans can do—THINK and take action.
What does CAPA stand for?
CAPA is an acronym for Corrective and Preventive Action.
What is Corrective and Preventative Action (CAPA)?
Simply defined, corrective action prevents the recurrence of an undesirable or harmful event or result that has already occurred. These are, therefore, reactive in nature. These could be errors or nonconformances (problems) in a product or a process. A preventive action operates in a similar fashion but deals with potential problems and therefore is proactive or pre-emptive.
This comes into proper focus when you consider the definition of a product as “the result of a process.” This is an axiom and can be used as a concept throughout the enterprise in not only products but in anything of interest. Consider that Profitability or Earnings are likely the ultimate results that most organizations are interested in. It then becomes clear that CAPA is focused on working on the process(es) that produced the product and not the product perse.
What is the Purpose of Corrective and Preventative Action?
Corrective and preventative actions are designed to be implemented on an organization’s processes, not an underlying product. The purpose is to identify a problem and determine its root cause, which is the process(es) that produced the product. A plan is developed to address the problem and implemented.
Monitoring the plan’s actions and results aid in determining if the plan was successful at eliminating the underlying root cause of the problem.
A good Corrective and Preventive Actions program, therefore, will gradually improve the entire organization. It is the essence of a Continuous Improvement (CI) process. CI processes have been around since the beginning of the 20th century and got dramatic visibility with the Six Sigma process. The fundamentals of Six Sigma and CAPA are similar.
What is the Difference Between a Corrective Action and a Preventative Action?
- Corrective action is performed after a nonconformity or series of nonconformities have already occurred.
- Preventive action is a process involving planning, with the planned result of preventing a nonconformity before its occurrence.
Why is it Important?
The difference between Corrective Action and Preventive Action is the same as being Reactive or Proactive. The process steps are the same once the problem is identified and defined.
A management system that only depends on Reactive actions will not be as comprehensive a Continuous Improvement System as one that includes Proactive actions. It is, therefore, important to recognize the difference and then have subsystems for problems that have already caused damage, as well as forecast those that could happen in the future. The only difference is how the problems are detected and defined.
What is a CAPA Management Process?
The best way to understand this is to consider the different steps that make the process complete. These are:
- Detect the problem/Opportunity. An enlightened way of looking at a “problem” is to understand and accept it as an “Opportunity.” “Risk Based Thinking or RBT” processes can help in this.
- Although not included in the pure CAPA process, it is good practice to note the “Containment Actions” taken to ensure that the problem is prevented from contaminating a good product.
- Define the Opportunity in a manner that will enable it if the Opportunity has been achieved. This is called the “Effectiveness” of the process.
- Evaluate if the Opportunity is of a magnitude that warrants the expenditure of resources to change the current process(es). RBT can help at this step, too. Based on this evaluation, a decision needs to be made on whether to proceed or not. If, for example, the Opportunity is worth $1000, it would be quite acceptable to reject it if the cost amounts to $2,000.
- In such cases, the organization needs to ensure that there are processes in place to detect occurrences of the problem. In the case of commonly manufactured products, this method is “Inspection.” Products that fail inspection (rejects) then need to be quarantined and disposed of in an appropriate manner, such as rework, scrap, etc.
- The following steps are those that need to be taken for the execution of a CAPA.
- Perform a Root Cause Analysis (RCA). Remember that frequently there is more than one cause. The purpose of RCA is to identify the processes that need to be changed/ improved so as to eliminate the causes.
- Develop a plan to eliminate the causes. Remember to include the tests that need to be done to determine if the CAPA has been effective.
- Implement the plan.
- Determine if the CAPA has been effective. Risk Based Thinking can help at this step too. The ideal goal of a CAPA management process is to ensure the problem can never be experienced again. While this is a laudable goal, it may not be reached 100%. That is why RBT is a good tool to use to face reality.
- Determine if the CAPA should be followed up after a period of time to be sure that it was indeed effective. This is similar to an Accounting process called “Post Audit” in the case of major expenditure projects.
- It is good practice to form a team for each CAPA, and then celebrate success with the team. You might recognize that a good CAPA is a project, after all.

What is a Corrective Action Plan?
This is Step #5 in the above CAPA process. A corrective action plan is a proposal that seeks to achieve an intended outcome for a resolution or elimination of undesirable activities or results. The plan should set forth who the acting parties are and what action each party is to perform to correct the underlying undesirable action or result. Additionally, the plan should address the recording of all actions undertaken.
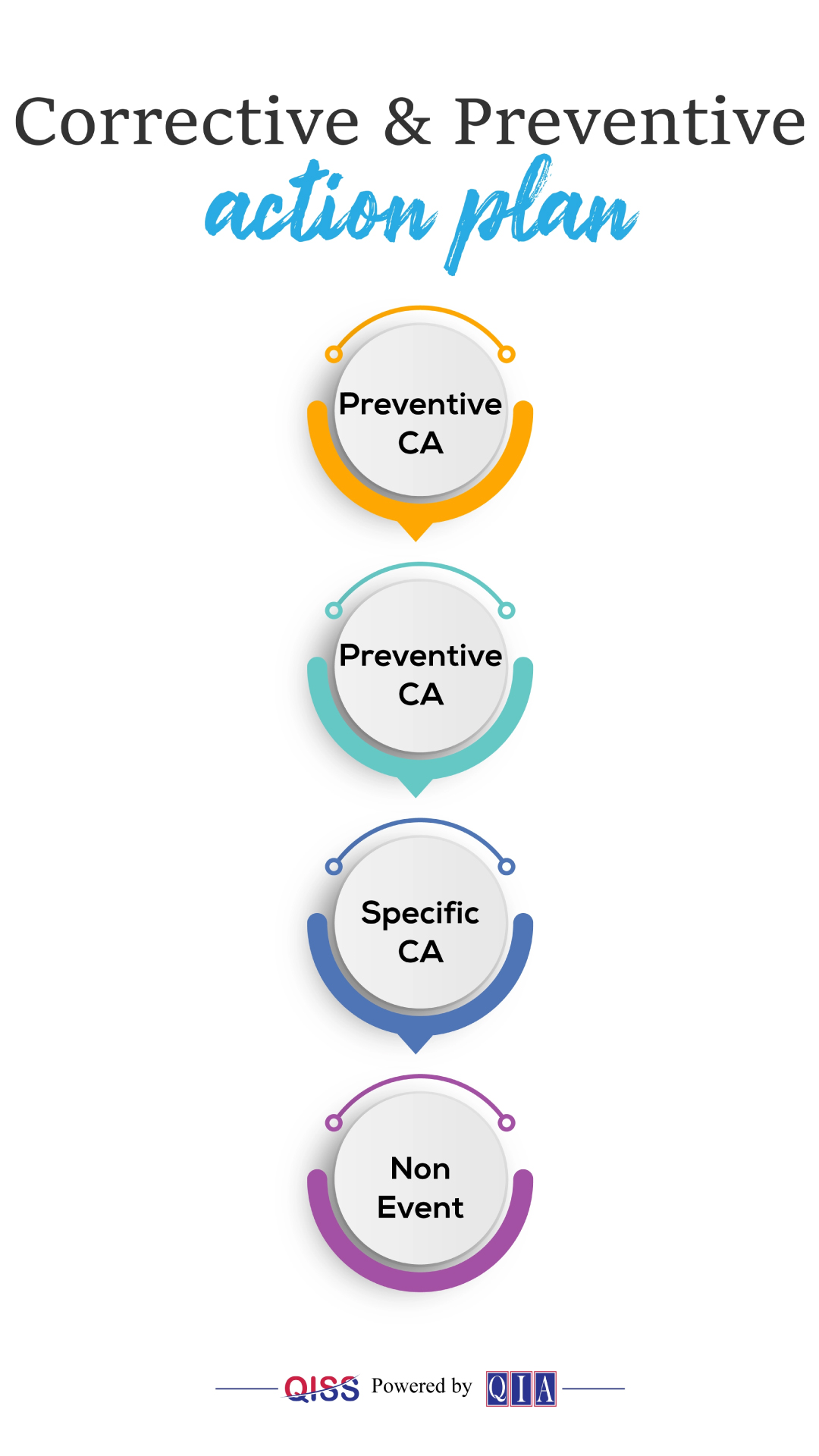
How to write or create a Corrective Action plan?
Also referred to as the “Solution”
Key Components:
- A set of planned activities (actions)
– It will always be a set of groups of actions.
– Corrective actions are specific and preventive in nature.
- Implemented for a purpose
– If nothing changes, the results will be the same.
– Set the activities into positive actions to change or improve the effects with what you discovered in Root Cause Analysis.
- Specific corrective action: Actions taken to correct or improve the condition noted in the event by changing the direct cause or the direct cause and the effect.
– Stopping a process until preventive, corrective actions can be applied is a form of specific corrective action! It temporarily stops the direct cause from operating, but it does not provide an acceptable long-term solution.
- Preventive, corrective action: These are actions that prevent the recurrence of the condition noted in the event. Preventive, corrective actions focus on preventing the root cause and preventing any contributing causes.
The above description should be used for high-risk candidates. Simpler methods will suffice for simpler candidates. It all starts with a Risk Assessment and ends with a Risk Assessment. The start of the Corrective Action plan is the Cause Analysis. Typically, for High-Risk situations, the Cause analysis will yield a network of causes: Direct, Contributing, and Root. Each one of these needs to be addressed in the plan.
How to write or create a Corrective Action plan?
A Corrective Action Request or CAR is a document that notifies the recipient, such as a manufacturer or supplier/provider, that an issue or problem with a product process or service has been identified and seeks to have the recipient provide a solution to correct the problem and eliminate it from recurring.
Why are Corrective & Preventive Actions Important in a QMS?
The entire purpose of having a QMS -Quality Management System is to develop, implement and operate a system that will help an organization run smoothly, in a productive manner, and produce products that will achieve customer satisfaction. All the elements of an organizational structure are involved, except perhaps the Tax Accounting piece. The guiding principle is the PDCA cycle. This principle has the reputation of being the single structure that pulled an entire nation (Japan) out of the destruction of WW2 into becoming one of the best economies of the world.
PDCA is the essence of a QMS and also the essence of Continuous Improvement. Corrective & Preventive Actions provide the “A” in the PDCA cycle. When you study a QMS standard such as ISO 9001 (which is the base for almost all other standards), you can see the P, D, and C components. The CAPA rounds it up for the organization.
Features of QISS Corrective and Preventive Action (CAPA)
Since 1994, the Quality Institute of America (QIA) has curated and developed the Best Practices (BPs) that people can use in the field of Quality, Health & Safety, and Environment. QIA has helped clients on two continents enhance their productivity through these BPs. Since 2004, QIA’s QISS software has automated these BPs so organizations can more efficiently and effortlessly utilize these BPs. This has been done through 30 modules in QISS. One of them is CAPA which is the engine of Continual Improvement. CAPA module offers the following features for use:
- Ability to initiate CAPA from existing NCR or from an identified risk
- Ability to initiate internal, supplier, or customer CAPAs
- Ability to add custom fields
- Ability to save current work so that it can be completed later
- Ability to assign supplier representative to complete activities for a supplier CAPA
- Ability for a customer representative to initiate CAPAs
- Ability to assign a responsible person for each CAPA
- Ability to control what CAPA steps need approval before completing the following step
- Ability to control approvers for each CAPA step.
- Charts & Reports
- Advanced search feature to filter out records by specifying multiple match criteria
- Ability to undo the last action
- Ability to edit CAPA
- Two-step CAPA deletion process. A CAPA needs to be obsolete before deleting it.
- Ability to add discussion notes and any relevant file attachments anytime a CAPA is open
- Ability to email CAPAs and associated records to preferred recipients
- Dashboard to view pending assignments.
- Ability to initiate CAPA from “Audit” and “HSE” reports
- Ability to manage “Risk Management” using FMEA or ERM method.
- Ability to configure RPN matrix or Risk Score.
- Ability to record revised RPN with a contingency plan
- Audit Trail
The above features help organizations achieve the following functions:
- Evaluate, and approve the need for CAPA through a logical Risk Assessment process
- Manage the identified CAPA as a project unique to the particular Risk.
- Assign, monitor, and record the progress of the CAPA to completion.
- Automatically record each step.
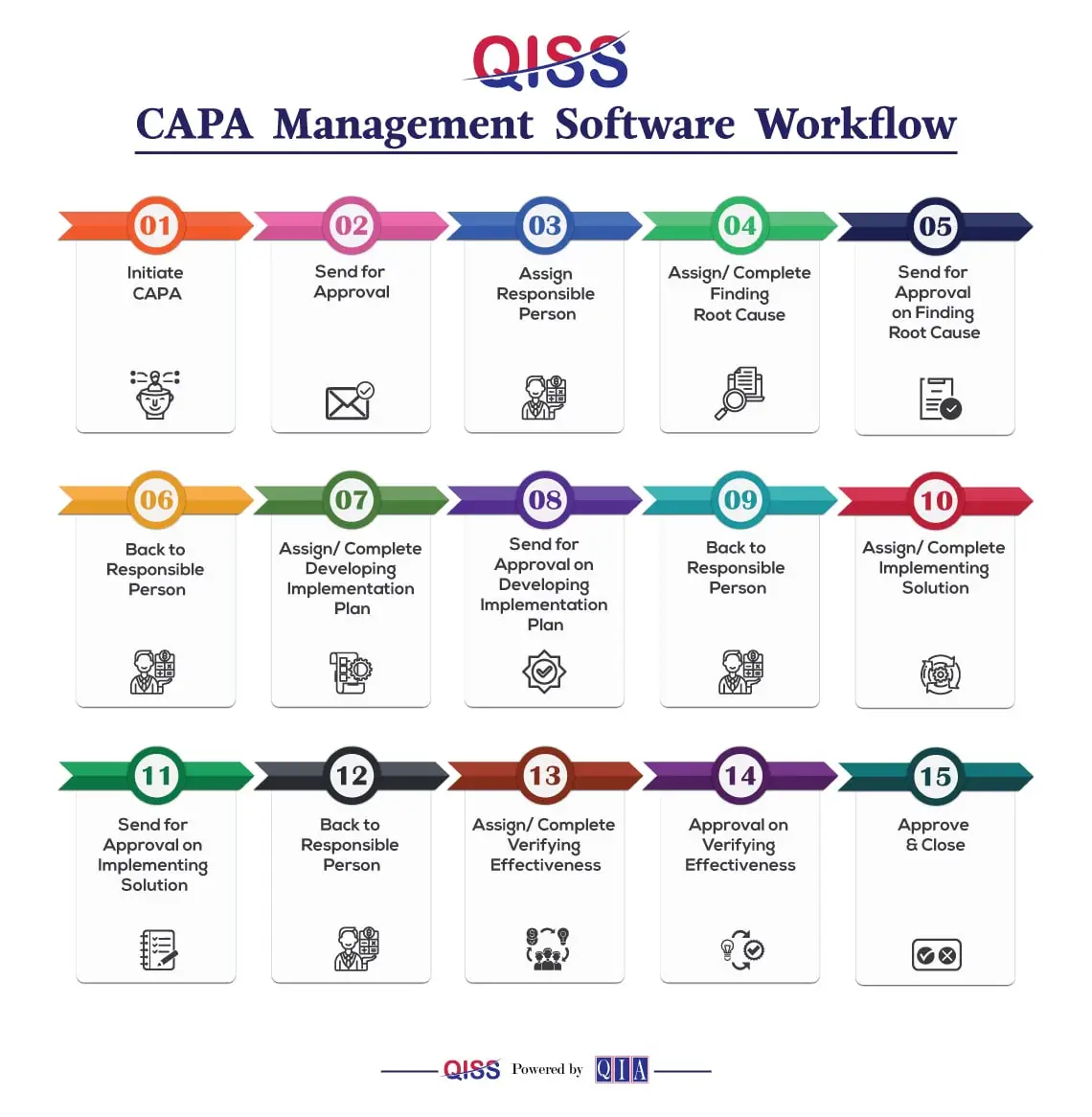
Benefits of QISS Corrective and Preventive Action (CAPA)
As explained above earlier, QISS- CAPA provides the Action step in the famous PDCA (Plan Do Check Act) process. The rest of QISS provides the PDC steps.
In addition, QISS-CAPA provides a mechanism to evaluate Risk, mitigate it, and prevent any consequences in the future.
QISS-CAPA uses the powerful Microsoft Dot-Net database to store, manage, and utilize the data created over the years to help Management take their organization to greater heights in a systematic, deliberate and continuous manner.
QISS-CAPA provides links with Nonconformities, Suppliers, Customer complaints, Internal Audits, and Risk Management.
Humans have made steady improvements in their work processes since the end of the 19th century through three Industrial Revolutions. We are now in the Fourth Revolution. Each one has seen different groups and versions of human labor being made unnecessary and even obsolete. The Fourth one is targeting Mental Labor. The key is to Eliminate Waste. QISS-CAPA’s vision and mission are to help Management compete and win the race and become more productive and profitable.
QISS can provide the CNS (Central Nervous System) for your QMS. Talk to us, and we will show you how. Thanks for your Time.