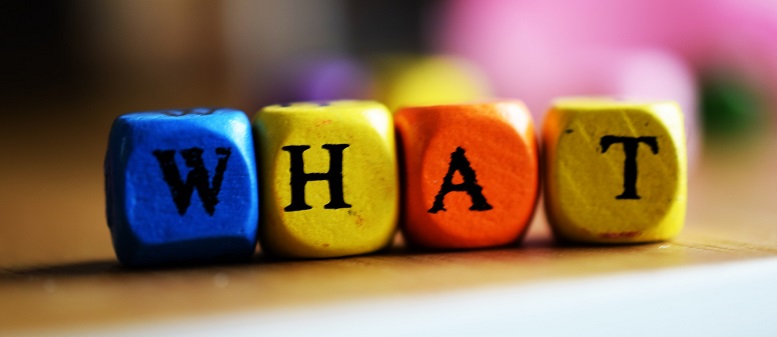
CAPA is the acronym for Corrective and Preventive Action. CAPA’s planning, organizing, directing, and control is called CAPA management.
CAPA is a crucial concept in the whole sphere of a Quality Management system (QMS) and lies at the core of all QMS processes.
In its simplest form, CAPA means that after you have found a deviation or a non-conformance, you work on finding the root cause. After determining the root cause, the actionable point is to take Corrective Action, which means you fix the problem that led to the deviation. Corrective Action is fixing the immediate problem so that the operation of the process can continue without a significant loss of time.
However, one must look beyond an immediate fix, and one has to make sure that the same kind of non-conformance does not recur in the future. To prevent that kind of deviation or non-conformance is known as preventive Action. CAPA is crucial for meeting the requirement of the ISO standard and following the regulatory body’s stipulations.
Investigating the cause of the non-conformance and correcting it is at the core of product quality.
When CAPA is appropriately implemented, it enhances customer product quality, leading to enhanced customer satisfaction.
A customer that is satisfied is at the core of any business. Keeping your customers satisfied ensures that your customer stays with you and gets repeat purchases.
CAPA Management is also critical to any QMS effectiveness in continual improvement. When a deviation is identified, and a CAPA is initiated, your QMS moves to a higher level. You have a new process where slips of the kind that took place in the past would not happen again.
There are eight steps of CAPA Management.
- Identification of the issue
- Investigation of the failure
- Analysis of the root cause
- Possible solutions
- Identifying the best solution
- Planning the resolution
- Implementing the plan
- Follow up and review
One of the important things to evaluate in any CAPA Management system is the risk involved. The higher the risk associated with the non-conformance, the more immediate the need for Action in CAPA Management.
Choose suitable software for your business from QISS essential software list. We are always ready to provide you ISO-based QMS services through QISS QMS software.