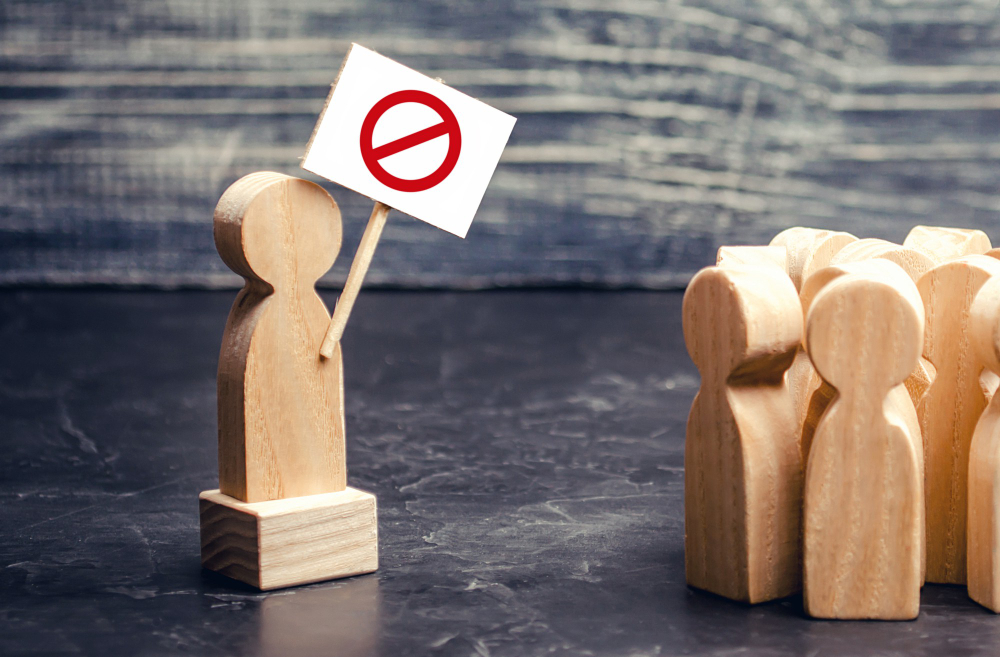
As a Quality Manager, distinguishing between the terms non-conformity and disconformity is crucial for accurate problem identification and effective quality control. While both terms relate to deviations from set standards, understanding their subtle differences can significantly improve your ability to address issues, ensure compliance, and uphold product or service excellence.
In this article, we will break down what non-conformity and disconformity mean in the context of quality management, explore their key differences, and discuss why this distinction matters for your quality assurance processes.
What is Non-Conformity?
Non-conformity refers to a situation where a product, service, or process fails to meet defined standards, specifications, or requirements. It’s a broad term used to describe any deviation from the expected outcome that doesn’t align with established criteria. Non-conformities can occur at any stage of production or delivery, and they often require corrective actions to bring the process back into compliance.
Non-conformities are typically more serious and require immediate attention, as they can impact the overall quality and functionality of the product or service. For instance, if a manufacturing process produces faulty parts that don’t meet the required dimensions, this is considered a non-conformity. Similarly, if a service fails to meet agreed-upon customer expectations, this could also be classified as non-conformity.
Check our comprehensive non-conformance guide to know more.
What is Disconformity?
Disconformity, on the other hand, is a more specific and less severe deviation. It describes a situation where something doesn’t fully meet the standard, but the deviation is not critical or doesn’t significantly affect the overall quality. Disconformities are often seen as minor deviations, where the product or service is still acceptable but slightly off from the ideal.
For example, a disconformity might occur if a product has a small cosmetic flaw that does not impact its functionality or safety. Another example could be a service that falls slightly short of customer expectations, but the difference is not enough to cause dissatisfaction or a negative impact.
In short, disconformity typically refers to issues that are less critical and may not require immediate corrective actions, but still need to be monitored and potentially corrected in the future.
Key Differences Between Non-Conformity and Disconformity
Severity of Deviation
- Non-Conformity: A serious deviation from established standards or requirements that often results in a product or service being unfit for use or delivery. Non-conformities often demand corrective actions to bring the process back into compliance.
- Disconformity: A minor deviation that is usually not critical and does not significantly impact product functionality, safety, or customer satisfaction. It may require corrective action, but the impact is generally less urgent.
Impact on Quality
- Non-Conformity: Non-conformities have a higher likelihood of negatively affecting the overall quality of the product or service. They typically disrupt the entire system, requiring prompt intervention.
- Disconformity: Disconformities may affect product quality to a lesser extent. While they still deviate from standards, they generally do not compromise the overall performance or safety of the product or service.
Action Required
- Non-Conformity: Requires immediate corrective and preventive actions (CAPA) to fix the issue and prevent recurrence. Non-conformities often necessitate a full review of processes and may involve rework or scrapping of the affected products.
- Disconformity: Often does not require urgent corrective actions but should still be addressed to ensure continuous improvement. Disconformities may be tracked for future consideration in audits or process refinements.
Customer Impact
- Non-Conformity: Non-conformities often result in customer dissatisfaction, potential returns, recalls, or warranty claims. These deviations can negatively affect customer trust and brand reputation.
- Disconformity: Disconformities are usually less likely to result in customer complaints or dissatisfaction. However, if not addressed over time, they could accumulate into larger issues.
Why Understanding the Difference Matters in Quality Management?
Efficient Resource Allocation
Understanding the difference between non-conformity and disconformity helps allocate resources more effectively. Non-conformities demand immediate corrective actions and more extensive resources, whereas disconformities may only need minor adjustments or long-term process improvements.
Improved Risk Management
Non-conformities pose a higher risk to product quality and customer satisfaction. By identifying them quickly and addressing them promptly, you minimize potential damage to your reputation and ensure regulatory compliance. Disconformities, while still important, are typically less urgent and require less immediate attention.
Compliance and Audit Readiness
Both non-conformities and disconformities need to be documented for compliance purposes, but non-conformities often require more formal corrective actions and detailed reporting. Understanding the difference ensures that your team stays prepared for internal audits and external inspections, minimizing the chance of compliance violations.
Continuous Improvement
Whether it’s a non-conformity or a disconformity, both types of deviations present opportunities for continuous improvement. By categorizing and understanding each issue, you can prioritize actions, prevent future problems, and build a stronger, more reliable process.
How to Manage Non-Conformity and Disconformity?
Establish Clear Quality Standards
Having clear, well-defined standards in place is crucial for distinguishing between non-conformity and disconformity. These standards serve as the baseline against which you measure products, services, and processes.
Use a Corrective and Preventive Action (CAPA) System
Implement a robust CAPA system to handle non-conformities efficiently. For disconformities, you may need to adjust processes or procedures over time. Both types of deviations should be logged, analyzed, and followed up on to ensure continual improvement.
Monitor and Track Issues
Use QISS quality management software (QMS) to monitor non-conformities and disconformities. Regular tracking allows you to identify recurring issues and trends that can be addressed proactively, rather than reactively.
Engage Your Team in Quality Assurance
Foster a culture of quality within your organization where employees are encouraged to identify and report both non-conformities and disconformities. This proactive approach helps minimize defects and ensures that issues are caught early.
Conclusion: Why Both Matter in Quality Control
While non-conformity and disconformity are related, understanding their differences helps you take the right approach to managing quality issues. Non-conformities often require immediate corrective actions and pose greater risks to your product’s success, while disconformities are typically minor deviations that should still be addressed over time to maintain continuous improvement.
By effectively managing both non-conformities and disconformities, you ensure that your products and services consistently meet the highest standards of quality, which builds trust with customers, enhances operational efficiency, and reduces the risk of costly mistakes.
Mastering these distinctions is essential for any Quality Manager looking to maintain a robust quality management system that not only meets but exceeds expectations.