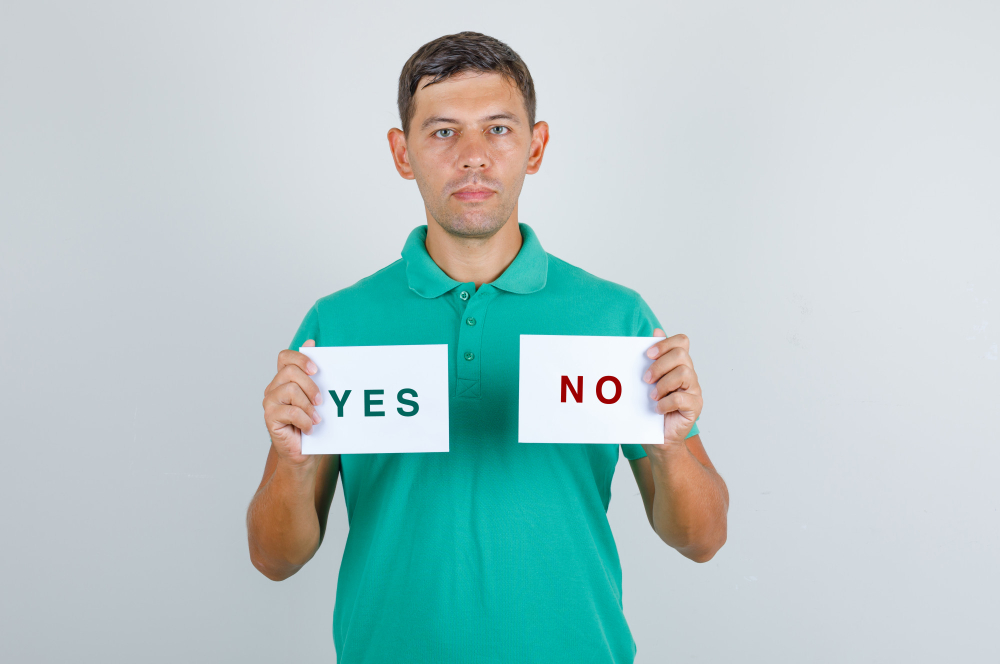
If you’ve ever worked in a regulated industry—manufacturing, healthcare, aviation, or even food production—you’ve probably heard the term “non-conformance.” It’s a deviation from a standard, a procedure gone sideways, or a result that doesn’t meet expectations. Reporting these issues is critical for quality, safety, and continuous improvement.
But let’s be honest: sometimes, non-conformances slip through the cracks. They go unreported, undocumented, and unresolved. Why? Let’s unpack the real, human reasons behind this gap—and why fixing it matters more than you might think.
Reasons Not to Report Non-conformances
1. Fear of Blame: “Will I Get in Trouble?”
Let’s start with the elephant in the room: no one wants to be the messenger who gets shot. In many workplaces, admitting a mistake—or pointing one out—feels risky. Employees worry about repercussions: “Will my manager think I’m incompetent?” “Could this hurt my performance review?” This fear isn’t irrational. Studies show that people could believe that the goal of submission was to criticize them rather than to identify systems issues.
The Fix: Foster a “just culture.” Leaders must actively separate human error (a normal part of work) from recklessness (a choice to ignore rules). Celebrate transparency. For example,NASA’s ASRS, which allows anonymous reporting of aviation safety issues, has shown that non-punitive reporting systems increase incident disclosures by 300-500% in aviation.
2. “It’s Too Complicated!”: Overly Bureaucratic Processes
Ever faced a 10-page form just to report a minor issue? When reporting feels like solving a Rubik’s Cube, people avoid it. Complicated systems send a subtle message: We don’t really want to hear about this.
The Fix: Simplify. Use user-friendly tools—think mobile apps, quick-drop digital forms, or even a simple Slack channel. Toyota’s “Andon Cord” is legendary for a reason: anyone can halt production to flag an issue with one pull. Make reporting easy, and people will do it.
3. “I Didn’t Know It Was a Problem”: Lack of Training
Sometimes, non-conformances go unreported because employees don’t recognize them. Without proper training, a misstep might seem like “just how things work.” For instance, a new lab technician might not realize that calibrating equipment 5 minutes late violates a critical protocol.
The Fix: Invest in regular, engaging training. Use real-world examples and simulations, such as introducing “What’s Wrong Here?” workshops where teams analyze past errors and an instructor explains the issues.
4. “We’ve Always Done It This Way”: Normalization of Deviations
Humans are creatures of habit. When a small deviation becomes routine—like skipping a safety check to meet a deadline—it stops feeling like a problem. This “normalization of deviance” is insidious. Remember the Challenger disaster? Engineers had grown accustomed to O-ring issues… until tragedy struck.
The Fix: Encourage fresh eyes. Rotate team members, bring in auditors, or host “process hackathons” to challenge assumptions. Ask: If we were starting from scratch, would we design it this way?
5. “I Don’t Have Time!”: Workload Pressures
In fast-paced environments, stopping to report a non-conformance can feel like a luxury. “We’re already behind—just fix it and move on!” But shortcuts create long-term risks.
The Fix: Integrate reporting into daily workflows. Such as a 2-minute “pause and reflect” ritual which can increase dedication, productivity and build positivity.
6. Leadership Lip Service: When Priorities Don’t Align
If leaders preach quality but reward speed above all else, employees get mixed signals. A sales team praised for hitting targets might ignore minor compliance gaps to keep clients happy.
The Fix: Align incentives. Recognize and reward those who speak up.
7. “Why Bother?”: No Feedback Loop
Imagine reporting an issue… and never hearing about it again. Without feedback, people assume nothing changes. Over time, they stop caring.
The Fix: Close the loop. Share updates like, “Your report about X led to a new training program—thank you!” Even small acknowledgments build trust.
The Bottom Line: Reporting Matters More Than You Think
Unreported non-conformances aren’t just paperwork problems. They’re ticking time bombs—for product recalls, safety incidents, or reputational damage. But fixing the issue starts with empathy. Understand why people stay silent, then remove those barriers.
Remember, a workplace where non-conformances get reported isn’t a “problematic” one—it’s a learning one. And that’s where true excellence begins.